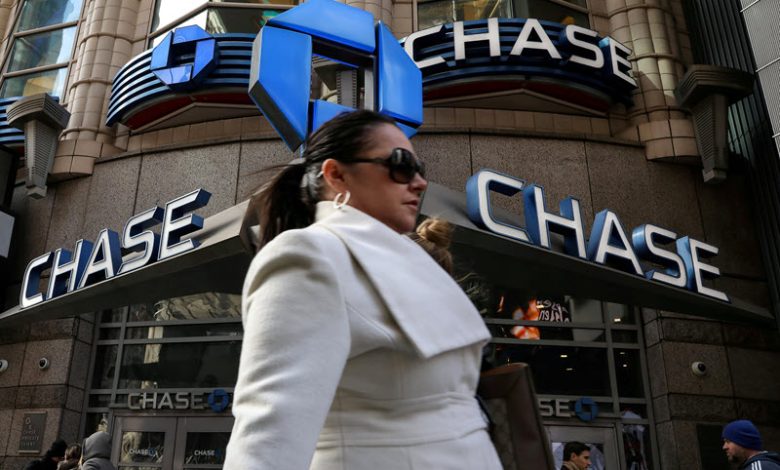
Analysts Predict India’s Economy Will Become Third Largest by 2027
India’s nominal GDP is projected to grow by 12.4% year-over-year in the fiscal year 2025, surpassing that of China, the US, and the Euro Area, as outlined in a recent Morgan Stanley report. This growth trajectory positions India to potentially become the world’s third-largest economy, reaching a GDP of $5 trillion by 2027.
The report suggests that India’s contribution to global growth could increase from 10% in 2021 to 17% between 2023 and 2028, supported by an average annual growth rate of 6.6% during the fiscal years 2024 to 2028. Key drivers of this remarkable economic performance include a rise in public capital expenditure (capex) and a notable increase in private capex.
Since 2019, policy reforms such as corporate tax reductions and the introduction of the Production-Linked Incentive (PLI) scheme have attracted investments and fostered structural growth. Although Foreign Direct Investment (FDI) inflows have seen a decline due to weakening global GDP and trade growth, India has managed to boost its share of global FDI from 2.4% in the fourth quarter of 2017 to 4.2% in the first quarter of 2023.
Analysts from JP Morgan have forecasted a slightly lower growth rate for India’s economy this fiscal year, estimating it to be between 5.5% and 6%, which is below the Reserve Bank of India’s (RBI) projected rate of 6.5%. Despite challenges such as elevated interest rates, geopolitical tensions, and sluggish demand, the analysts indicate that a growth rate of 5.5% would still represent a significant achievement for India in FY25.
The World Bank has echoed these concerns, estimating India’s GDP growth at 6.3% for FY24, following a growth of 7.2% in FY23. The RBI has maintained its GDP growth forecast at 6.5% for both FY24 and FY25, although it has revised its quarterly projections downwards for the upcoming fiscal year. Nomura also anticipates a slowdown in India’s GDP growth, predicting it will decrease to 5.6% next year from 5.9% in FY24.
Data for April to June indicated a 7.8% expansion of the Indian economy, which met economist expectations but fell short of the RBI’s 8% forecast. Observers note India’s significant reliance on global economic factors, arguing that domestic elements and private investment alone cannot sustain its growth.
Despite these challenges, RBI Governor Shaktikanta Das is optimistic that GDP growth for Q2 FY24 will surpass expectations, based on preliminary indicators, noting that this period represents the best global economic performance seen in a considerable time.